Maintaining electrical distribution equipment
Electrical distribution equipment is a broad term that encompasses a variety of equipment including, but not limited to, transformers, switches, disconnects, over current protection, controllers, the equipment to connect all these pieces and more. To further confuse the discussion, electrical distribution can include a range of voltages and currents. However, no matter the make up of a distribution system, every building or location that depends on electrical power will have a type of electrical distribution system to deliver the power from the local electrical supplier throughout the occupancy to each point of use component relying on electricity.
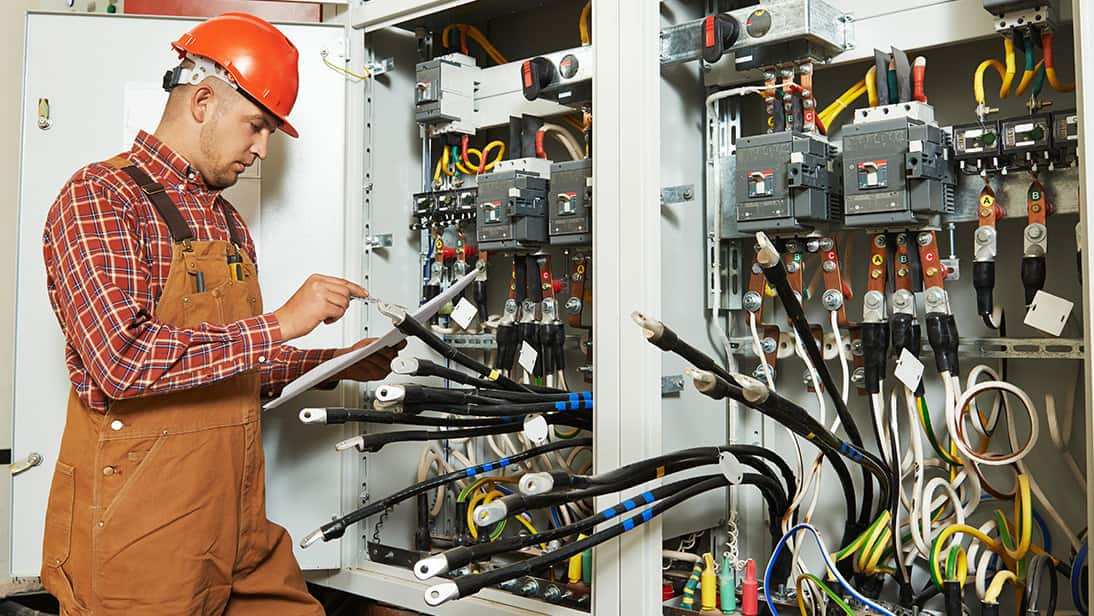
Physical damage to any of the components in an electrical distribution system can have severe impacts on your facility. Unfortunately, losses to equipment can be common. In fact, electrical losses account for 35% of commercial dollar losses and as much in the actual number of losses.1 In terms of residential losses, electrical losses account for 10% of all structure fires. This makes electrical the number one cause of property loss across the board whether commercial or residential.1 Electrical losses are just as severe even without a fire. In instances where no fire ensued, electrical breakdowns accounted for 51% of the number of losses in commercial properties.1 Without electricity spaces may become untenable, equipment will not run and operations will cease until the affected equipment can be replaced.
Any of these scenarios whether fire is involved or not, experience shows that a lack of maintenance is usually the root cause or a major contributing factor in the loss. The good news is whether it is the home you live in, the office you work in or the manufacturing facility you oversee, there are common maintenance considerations to keep equipment running.
The basics
There are four maintenance requirements for all electrical equipment no matter where it occurs in the distribution system:
- Keep equipment as cool as possible - Higher operating temperatures will breakdown the insulation systems and can reduce the lifespan of the equipment. In fact, a general rule of thumb is for every 10°F above normal operating temperature, the life of the equipment is halved.
- Keep equipment clean - Dirt and grime interfere with the equipment's ability to dissipate heat. Unclean equipment can also incur corrosion from the residues and if combustible, the dirt can supply a fuel source for any potential fire.
- Keep equipment dry - Moisture can not only lead to electrical shorts by giving the electricity another path of flow but can promote corrosion to any exposed metal components as well.
- Keep equipment components tightly connected - Loose electrical connections can lead to arcing and overheating.
Visual inspection
A variety of issues can be discovered and reported prior to a major loss occurring, simply by conducting a regular visual inspection. Additional items that should be considered are:
- Any unusual sounds
- Any unusual smells or smoke
- Any unusual vibrations
- Bulges in wires or equipment
- Leaking fluids
- Blistering paint
- Corrosion
- Loose components
- Check for and avoid storage on, next to or in front of equipment and panels
- Ensure temporary wiring and extension cords are an adequate gauge
Thermography
Thermography is the use of infrared thermal imaging to evaluate the surface temperatures of electrical equipment, connections, wires, etc. Abnormal readings, sometimes referred to as hot spots, may indicate conditions that need further investigation before a loss occurs. These conditions may include loose connections, unbalanced loads, overheating transformers, deterioration of insulation and other electrical issues. Qualified personnel should further investigate all hot spots.
It is important to note that infrared thermal imaging should only be handled by qualified personnel with experience in conducting the imaging, as well as interpreting the results. Additionally, imaging should be performed while the facility is operating at a normal load or demand. Without enough power flowing, issues may not present themselves.
Functional tests
Manufacturers recommend that circuit breakers and switches should be mechanically inspected and exercised annually. These devices may fail to operate smoothly due to corrosion, wear, misalignment or a lack of lubricant. Regularly exercising switches and breakers will help determine any issues that exist and can help ensure proper operation of these protection devices should an overcurrent condition occur.
Electrical testing
As the voltages and currents increase, particularly those at or over 600-volts, additional electrical testing should be incorporated into the maintenance program. These tests should only be conducted by trained and qualified personnel familiar with this testing. These tests include:
- Insulation-resistance testing
- Low-resistance and contact-resistance testing
- Current injection testing
Finally, when any major changes occur to a facilities electrical distribution system (addition of a utility feeder, adding or increasing the transformer capacity, the addition of any larger motors or other equipment, etc.) the facility should consider performing fault current and protection coordination studies. Contact us for a copy of the Hazard Guide on Electrical Preventive Maintenance and/or Risk Indicators for Electrical Switchgear.
Sources
1 Internal FM Data from publication P9702 – Maintaining Power Productivity: Preventing Electrical Loss