Writing larger manufacturing accounts
The insurance industry is undergoing many changes and for some companies it may involve the challenge of writing larger, more hazardous occupancies such as manufacturing facilities. While writing manufacturing accounts can bring in bigger premiums, they can also lead to increased exposures if not properly assessed. To make things even more complex, every location is different and presents a unique set of risks. The good news is there are general principles that will help assess the overall risk of new and unfamiliar occupancies.
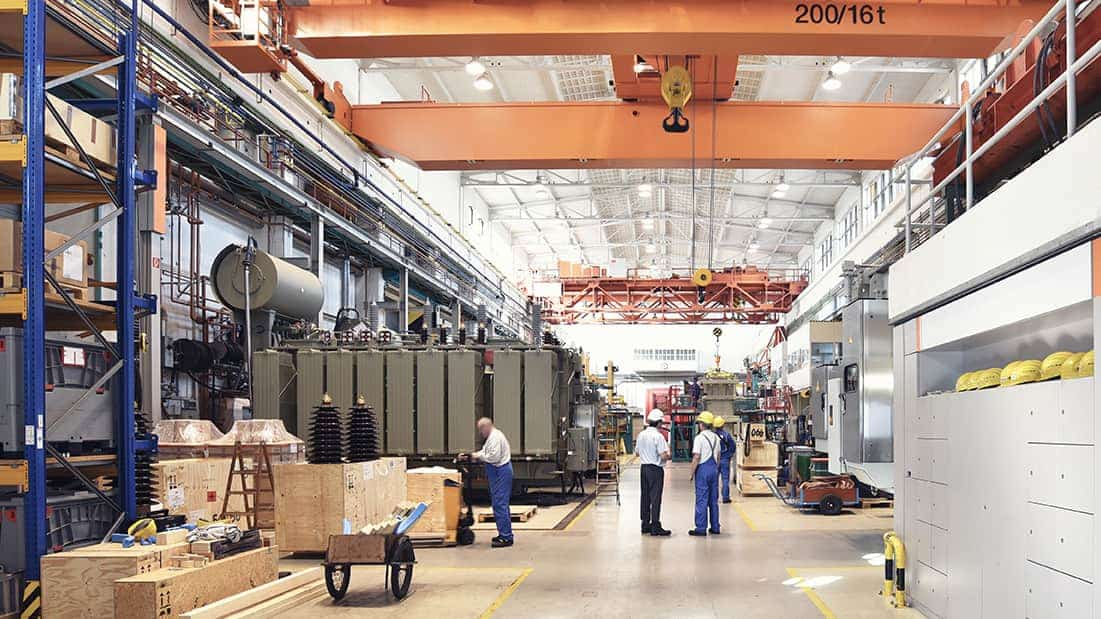
Having a good understanding of the occupancy is a critical first step. While manufacturing facilities will carry hazards like lighter occupancies, such as electrical systems, HVAC systems, housekeeping, etc., they also present additional serious special hazards including:
- Ignitable liquids
- Flammable gases
- Spray application of ignitable liquids and combustible solids
- Hydraulics
- Combustible dust
- Various storages
It is essential that these hazards are properly evaluated for risk assessment/mitigation and underwriting. Even common hazards, such as electrical, can be more complex. Larger accounts may have higher voltage equipment, multi-phase electrical systems and transformers that require a heightened level of maintenance and testing. In addition, equipment may be more expensive to replace, which could result in lengthy repair/replacement times.
Over the past two decades the industry has seen a trend towards utilizing loss control checklists that lack additional narrative or description of the occupancy. Those evaluating a property can simply mark off whether certain features or hazards exist. While these are fine for small and light hazard occupancies, they lack the detailed descriptions needed to accurately capture the complexities of manufacturing occupancies. Having an in-depth understanding of the location is vital before underwriting decisions, such as acceptability, retention and pricing, are made.
Storage presents a severe and often overlooked exposure for manufacturing facilities. Not only could these properties have large amounts of raw materials on hand, but attention must be paid to the finished product storage and, more commonly overlooked, work-in-process storage. Even small amounts of in-process storage can present a serious exposure, particularly when these areas are in manufacturing spaces that are not designed for any storage. Additionally, the storage of ignitable liquids, flammable gases and plastic commodities creates an even greater challenge due to their exceptionally high heat release rates (HRR). As with all storage, the arrangement of products plays an important role that must be understood as well. Things like rack storage, flue spaces and storage heights can intensify the hazards. A simple increase in storage height or blocked flue space could take a potential fire from being a controlled incident to a 100% loss.
Fire protection is a crucial part of any occupancy but especially with manufacturing. While all occupancies require a properly designed sprinkler system, protection becomes more critical in these challenging occupancies as the fire loading increases. As previously discussed, storage and other special hazards are common. To properly protect against these hazards, fire protection systems need to be adequately designed and maintained. Additionally, it is common for tenants of buildings to change from time to time and it is critical to evaluate the change in occupancies with the new tenant. An example would be a plastics manufacturing process moving into a building that once housed metal manufacturing. Plastic manufacturing is a considerably higher hazard compared to metal parts and analysis of the sprinkler system would be required.
Fire department response is another critical concern for manufacturing occupancies and many factors contribute to its effectiveness, including but not limited to:
- Early notification from a central station alarm system, if present
- Access to all sides of the building
- Effective pre-incident planning between the fire department and the facility
In addition to more robust electrical distribution equipment, manufacturing operations may utilize critical production machinery for their processes. Whether it is a simple milling machine, a metal extrusion line or a printing press, a breakdown event for even one piece of equipment could lead to a large loss scenario. If the machine is a bottleneck in the process, its loss could create a full shutdown of operations. Availability of a replacement or key parts, supply chain delays and extended repair times are factors that could lead to a significant business interruption claim, in addition to the cost to repair or replace the equipment. The plant should have a business continuity plan and contingencies in place to address this exposure. Understanding the facility’s process, equipment and how vulnerable it may be to an equipment breakdown loss plays an important role in evaluating the risk.
Overall, when transitioning to writing manufacturing facilities, the key to properly evaluating and underwriting these locations is a little more skill, some enhanced knowledge, a keen eye and asking a lot of questions. Each location is unique, and it is important to realize that although two locations may look very similar, they may have significant differences potentially bringing serious exposures. For example, while one plastics manufacturer might use an injection molding process with new, completely enclosed, automated machines carrying minimal hazards, another plastics manufacturer may utilize a completely different process that utilizes heptane, a flammable gas, and thus comes a with very high degree of associated hazard. Only when the processes, equipment and hazards are fully understood is it possible to properly quantify the exposures and successfully underwrite the location.