As Supply Chain Risks Mount, Clients To Get Deeper Insights
Eric Jones Vice President, Global Manager, Business Risk Consulting, FM Global
COVID-related upheaval may be behind us, but there’s no shortage of risk to global supply chains. In January 2024 alone, the world saw terrorism in the Red Sea, drought at the Panama Canal and piracy off the Somali coast. Geopolitical instability influenced oil prices, and natural hazards loomed around the world: There were 66 billion-dollar-plus (USD) natural disasters in 2023, well above the 21st-century average. Last year also happened to be the hottest year on record.
Our research indicates supply chain disruptions are not only more frequent these days but are also more severe, given the vast interconnectedness of global businesses and the temptation to keep supply chains lean.
Fortunately, at FM Global, supply chain risk-mitigation solutions are rapidly evolving thanks to new ways to use data. While we’ve always been a data-driven organization, we are now working toward making our data address the broad array of risks our clients face more quickly than ever.
AI increases speed to insight
We are actively developing tools that we anticipate will quickly deliver highly customized analyses of clients’ supply chain risks, potentially yielding actionable insights in days, not months. These analyses can employ artificial intelligence, machine learning and the data from our more than 60,000 annual engineering visits. We can combine these insights with information from our proprietary global flood map, the FM Global Resilience Index and tools from the world’s foremost supply chain visibility experts.
Our FM Global Supply Chain Impact Analysis has traditionally involved an in-depth fact-finding phase requiring onsite data gathering, interviews, supply chain mapping and financial analysis. Suddenly, AI can potentially do this arduous fact-finding process that large language models have done for text generation, providing a complete supply chain impact analysis with unprecedented speed and accuracy. This near-instant analysis may help clients more quickly react to threats and develop global mitigation strategies to enhance business continuity, resilience and long-term performance.
As with our traditional Supply Chain Impact Analysis, we will potentially be able to identify the properties and operations most integral to profit and most vulnerable to disruption. We may also be able to identify single-source suppliers, vulnerabilities, bottlenecks, redundancies and opportunities for cost-effective improvements. The analysis may reach beyond physical property risk, folding in comprehensive business data about suppliers, products, material categories, shipments and compliance activity throughout multi-tier supply chain networks.
Coverage for supply chain disruption
In addition to rapid, data-driven analysis, FM Global helps clients address supply chain risk through insurance products such as FM Global's Contingent Time Element Extended (CTEE) coverage. CTEE uniquely covers the entire supply chain, helping to keep business interruption to a minimum, no matter where in the world a company operates or how indirect the connection is to a loss. It’s the only contingent time element coverage that extends, without limit to the length of the supply chain, beyond direct suppliers and customers.
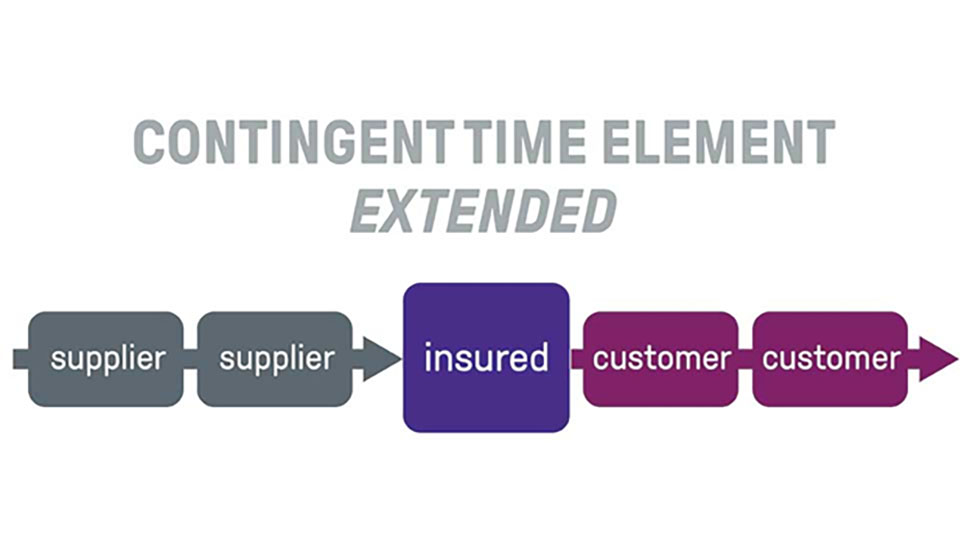
Our Logistics Extra Cost product similarly covers breaks in the distribution chain. Shipments can be rerouted quickly, and with the confidence that any extra costs have a place in the FM Global Advantage policy. Logistics Extra Cost is an innovative coverage that pays for extra costs to reroute a shipment if there’s damage to a transportation system—even if the goods shipped are insured by another company.
Although supply chain risks seem to be intensifying, so does business opportunity. We’re here to protect your business so you can prosper in the future. If you’d like to discuss new ways to protect your supply chain, your business and the overall value you bring to your customers, an FM Global client service team can help.
Learn more about FM Global's Supply Chain Risk Management ServicesRelated content:
FM Global’s Business Impact Analysis in action
Talison Lithium: Leading in lithium for the clean energy transition